HUID: The journey of developing a material from scratch!
- MUDRA
- Aug 24, 2021
- 3 min read
It isn't a standard thing, as I'm finding to develop a material/textile from scratch. Timelines are stretched, snapped and stitched by almost illusory forces. Innovation takes on multiple exciting but winding routes.
It is altogether exciting, frustrating and motivating to be working towards the development of HUID.
For those who aren't familiar, HUID is a material development project by Studio Mudra, where I am developing an onion skin based material that aims to subvert plastic and/or synthetic materials.

A test sample made from yellow onion skins. It is hard and has a smooth cork-like surface.
Image by Renuka Ramanujam
I've just been awarded a Climate Grant (check out the amazing work they're doing over here!) and with this generous support am kickstarting a new wave of research and development that will hopefully progress HUID further into a reality. I'm excited to share the journey as I go through these blogposts. This is the first in a long chain of exploration to come. I thought I'd start off with introducing why I chose the raw material of onion skins in the first place.
So...why onions?
They're pretty much everywhere in the world, an ingredient featured in an array of cuisines, and grown in different climates. China, India and the US are the biggest growers, with Iran, Brazil, Russia and Korea also making the top ten. In the UK, approximately 450,000 metric tons of onions are grown each year. With so many onions grown, sold and cooked, there are a lot of skins to account for that end up in compost. You may have noticed them to be quite hardy, so they tend to stick around for a while compared to their other organic counterparts in the compost pile.
After harvest, onions are separated into 'grades'. Much of what we see in supermarkets are the highly graded onions, passing the strict requisite tests in terms of aesthetics;
"Firmness and at least one complete skin are required, and skin cracking should not be evident"
"The bulb shape should be the globe, with only moderate variations: completely oval or very flat bulbs are not acceptable"
"Sprouting is not allowed in Class I, but early signs of sprouting are allowed in Class II"
(standards vary across the EU, UK and US, but some core elements are the same.)
Whilst the cream of the crop are bagged to be sent to the supermarkets, lower grades are sent to more industrial sites, either to make onion based products or for cattle feed. Skins naturally accumulate as waste at the factories as a result. I spoke to the Chairman of British Onions, the body representing onion growers in the UK. Around 200-400kg of waste skins are produced per week, and pretty reliably year round. Most of it is ground up to go to cattle feed. I did double check to see what effect this might have for our cows, but was assured they probably wouldn't miss ground up skins in their meal.
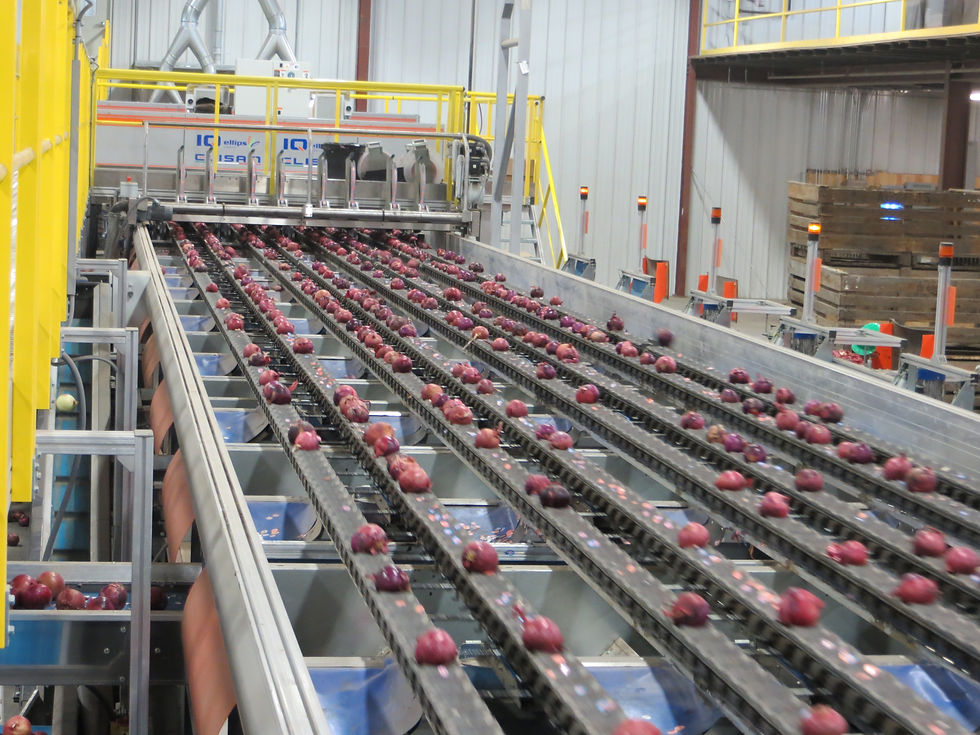
An automated onion grading system at work. These often grade first on size, but have since been adapted to spot fungal rot and aesthetic appearance.
Image by Ellips
Onion skins are therefore quite a plentiful waste source, not counting the tons that end up in the bottom of supermarket crates or in our compost piles.
Having consulted with scientists and designers it seems onions haven't been tapped into yet on a material level, which is what makes this project so very exciting! If we're talking biomimicry, what better to study than nature's own form of single use packaging? In fact there definitely is potential - a new study from researchers at the University of Florida indicates that compounds found in dry onion skins could be used as a coating to preserve fish for longer.
In the meantime, I've been able to jump into a small lab here in the Scottish Highlands with chemist Jaimey Tucker; right now we are at the early stage of understanding the material we are working with to figure out how to best treat it. This includes understanding what makes up the structure and surface of the onion skin at a microscopic level, so it can be smartly exploited to create this new material. Look out for the following posts where I'll share some research on the inner workings of the onion skin, and some of the results we are yielding here at the lab!

An early protoype of the HUID veneer made from red onion skins and casein.
Comments